Technologien und Prozesse bei ILFA: Anspruchsvolles HDI-Design in der Leiterplattenfertigung
Die Anforderung an hohe Schaltungsdichten in Kombination mit kurzen Signalwegen und geringem Platzbedarf kann in der Leiterplattenfertigung mit so genannten HDI-Leiterplatten realisiert werden. HDI steht dabei für „High Density Interconnect“ und spielt als noch relativ junge Technologie für die ILFA GmbH eine wichtige Rolle bei der Erfüllung anspruchsvoller Kundenvorgaben. Die zunehmende Miniaturisierung von digitalen Endgeräten geht mit gleichzeitiger Bestrebung nach immer höherer Leistungsfähigkeit bei fortwährend kompakterer Bauweise einher, was als technisch anspruchsvolle Herausforderung für die Hersteller entsprechender Leiterplatten angesehen werden kann. Eine Herausforderung, die wir natürlich gerne annehmen!
Ein solcher Fall ergab sich für ILFA durch eine Kundenanfrage für einen sequenziellen Aufbau mit 6 elektrischen Lagen, wie in Abbildung 1 gezeigt. Die Kundenanforderung beinhaltete 50 µm Line/Space auf allen Lagen in Kombination mit 300 µm BGA-Pitch auf den Außenlagen, sowie einem kleinsten Pad-Durchmesser von 150 µm.
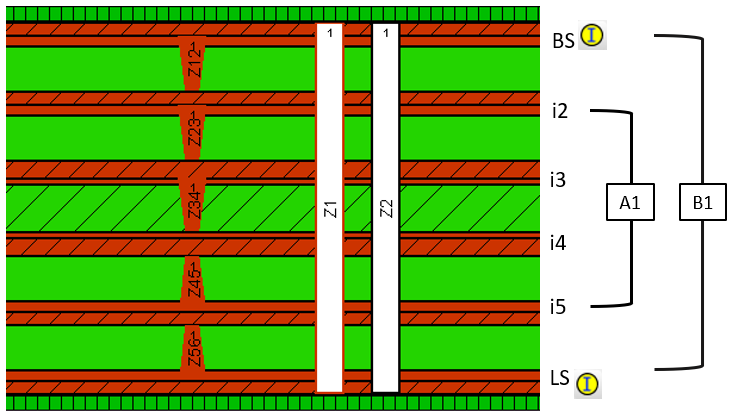
Die Durchkontaktierung wurde mittels 50 µm Laservias realisiert, um mit einer möglichst hohen Wahrscheinlichkeit das Zielpad der darunter liegenden Lage zu treffen. Der maximal erlaubte Versatz von maximal 50 µm zwischen Bohrbild und Leiterbild hatte zur Folge, dass hier neue Ansätze für die Registrierungssysteme beim Bohren und Belichten nötig waren. Die Einzelkartenausrichtung lieferte hier die genausten Ergebnisse mit einem Versatz zwischen Bohrbild und Leiterbild auf der gleichen Lage bis maximal 30 µm über die gesamte Fläche des Produktionsformats hinweg. Die 50 µm Laservias wurden mittels eines UV-Lasers umgesetzt. Das Ergebnis der gestackten Laservias ist in Abbildung 2 zu sehen. Durch die Einzelkartenbearbeitung konnten die Versätze auf ein Minimum reduziert werden.
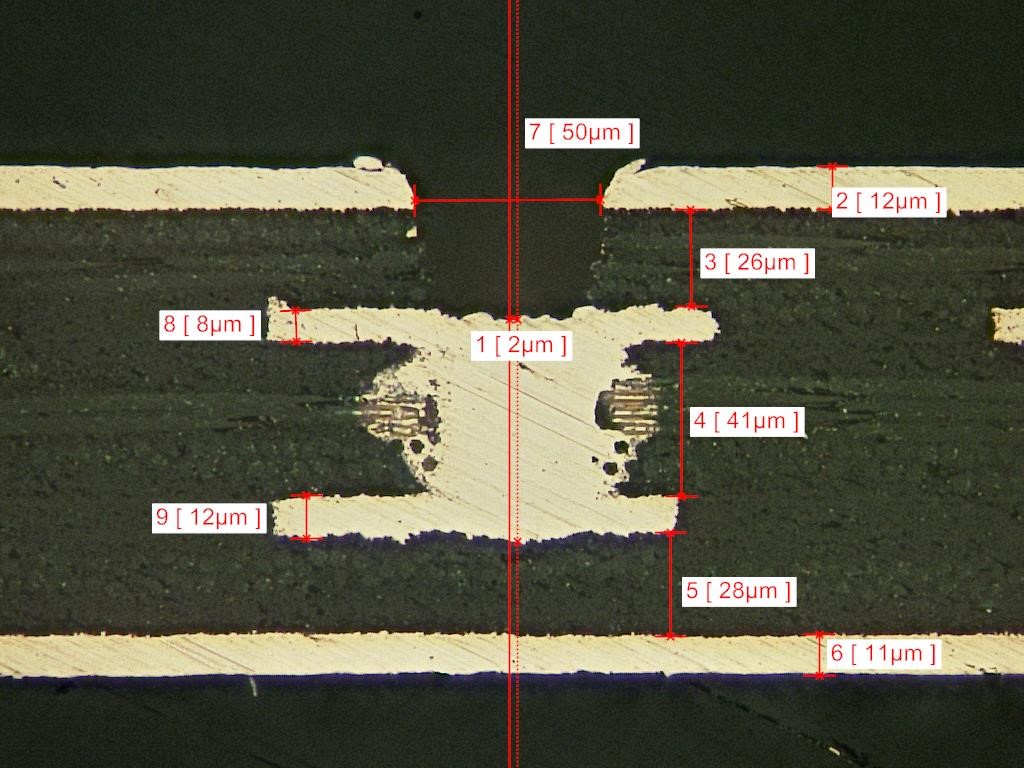
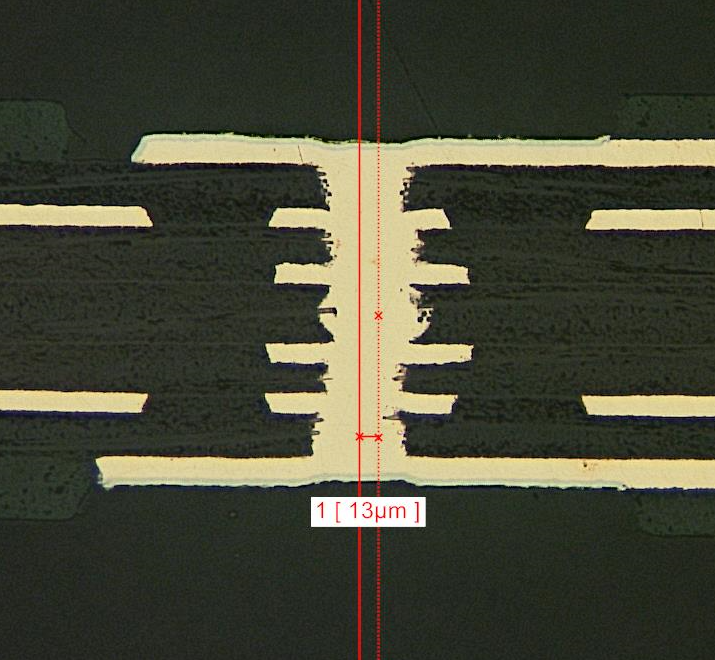
Für ein gleichmäßiges Ätzergebnis der feinen Strukturen im Leiterbild ist eine homogene Kupfer-schichtdickenverteilung auf der Oberfläche unerlässlich. Dies wurde durch einen speziellen galvanischen Abscheidungsprozess erreicht, wobei eine Gesamtdicke der Kupferschicht von 20 µm auch nach dem Copperfill nicht überschritten wird, und mit einer gemessenen Genauigkeit von +/1 µm abgeschieden wird. Das Via zwischen Lage 3 und 4 wurde mit dem THF-Prozess (Through Hole Filling) elektrolytisch gefüllt. Anschließend wird das Leiterbild strukturiert (Abbildung 3).
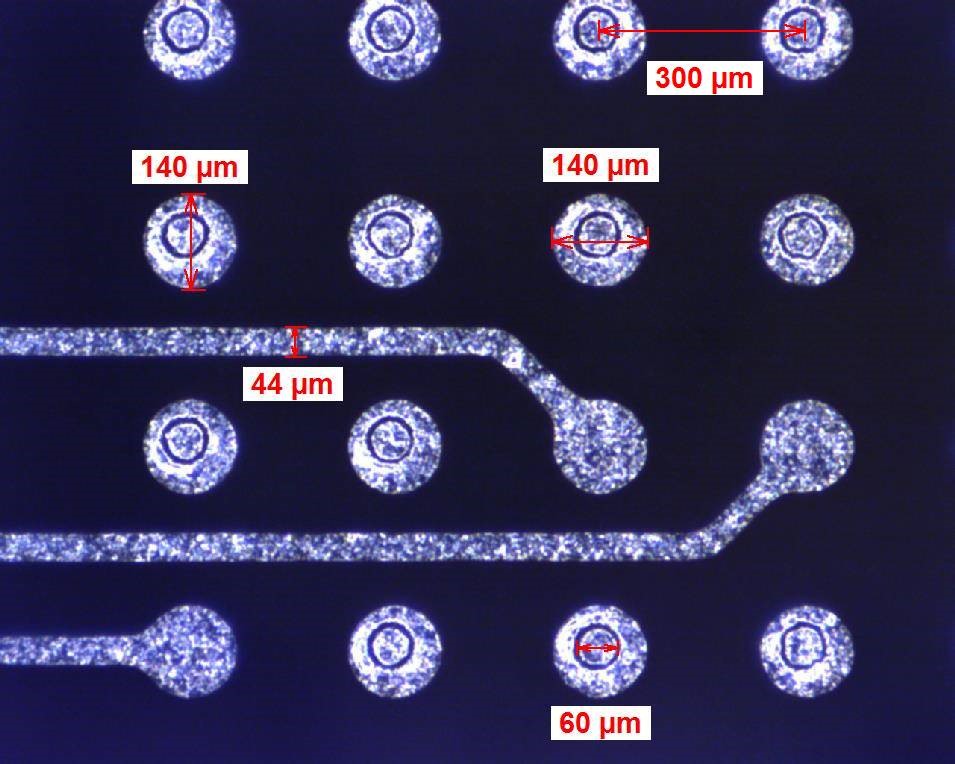
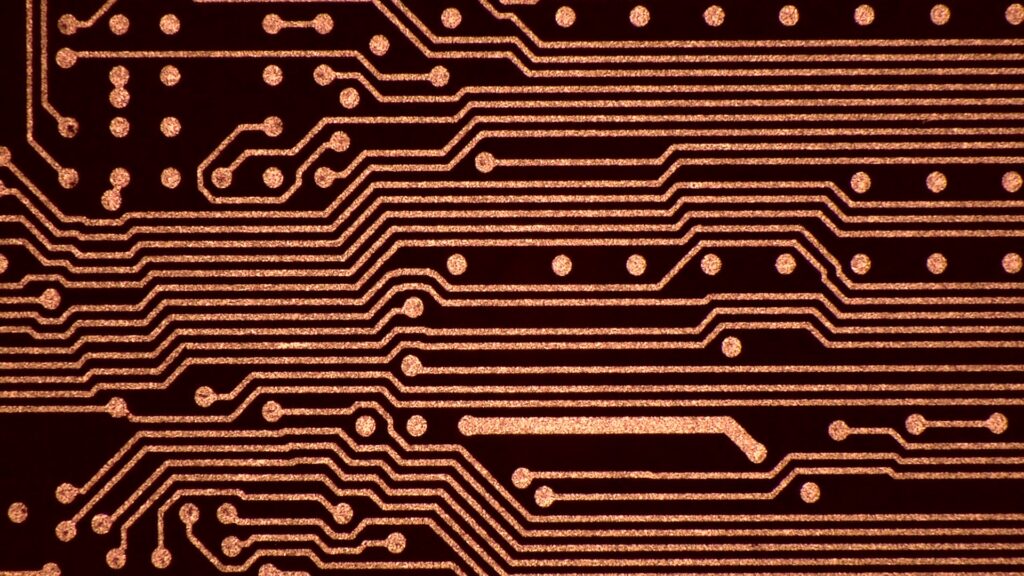
Nach der Fertigstellung des Leiterbilds wird die Lötstopplackmaske in einem Sprühverfahren appliziert. Hier stellen besonders die 150 µm Lackfreihaltungen im BGA-Bereich eine Herausforderung dar. Zu beachten sind insbesondere die Positioniergenauigkeit zum Leiterbild sowie die Konturschärfe nach dem Belichten und Entwickeln. Auch in diesem Fall wurde aus Gründen maximaler Belichtungsgenauigkeit auf Lokalausrichtung jeder Einzelplatine zurückgegriffen.
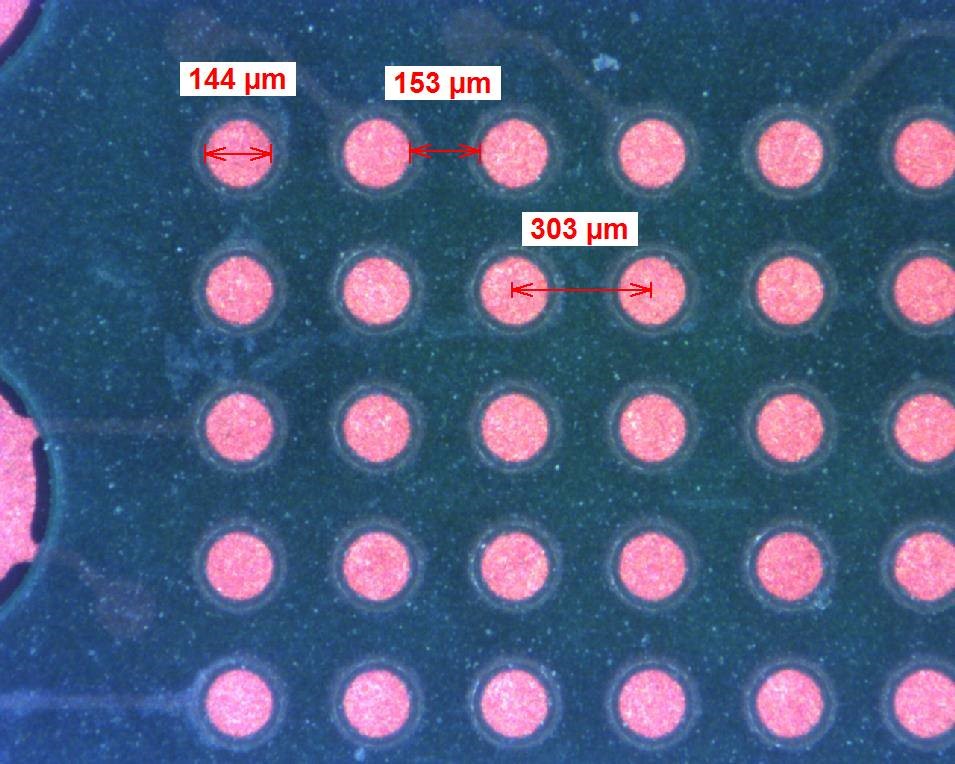
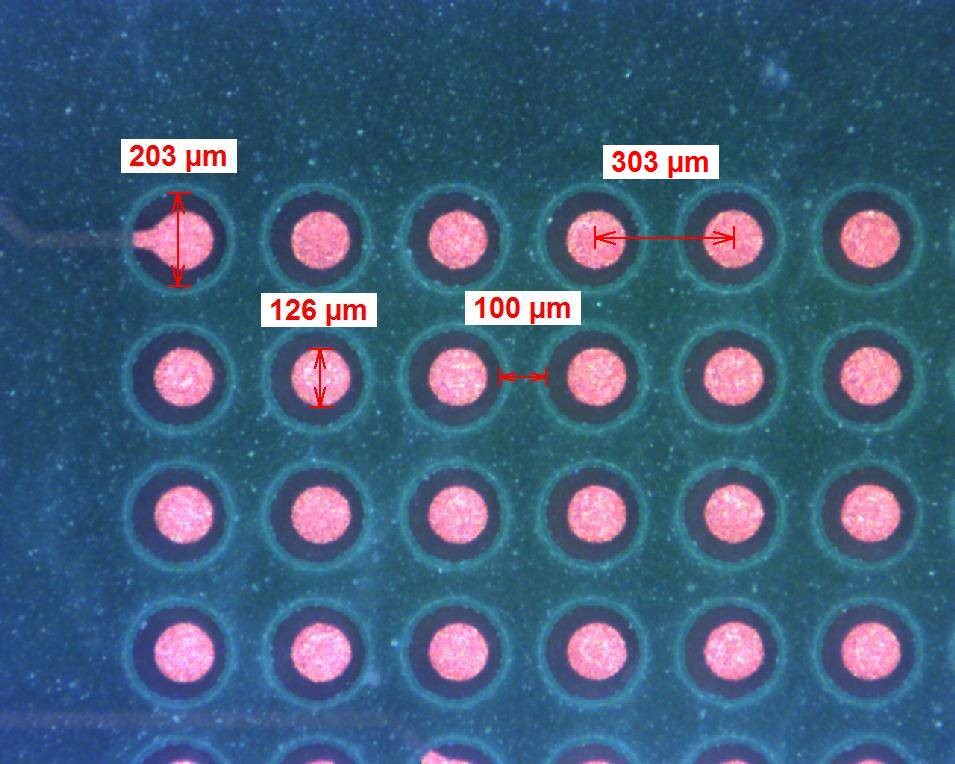
Um die Kupferoberfläche vor Oxidation zu schützen und die Benetzbarkeit der Anschlussflächen beim Löten zu erhöhen, wird abschließend eine Endoberfläche auf der Leiterplatte aufgetragen, in diesem Fall ENIG (Chemisch Nickel Immersionsgold) wie in Abbildung 5 gezeigt. Diese Schicht besteht aus 4,0 – 6,0 µm Nickel und einer 0,06-0,12 µm dicken Goldschicht. Aufgrund des chemischen Abscheidungsverfahrens und der absolut planen Oberfläche, eignet sich diese hervorragend für die Finepitch Anwendung bei dieser Leiterplatte.
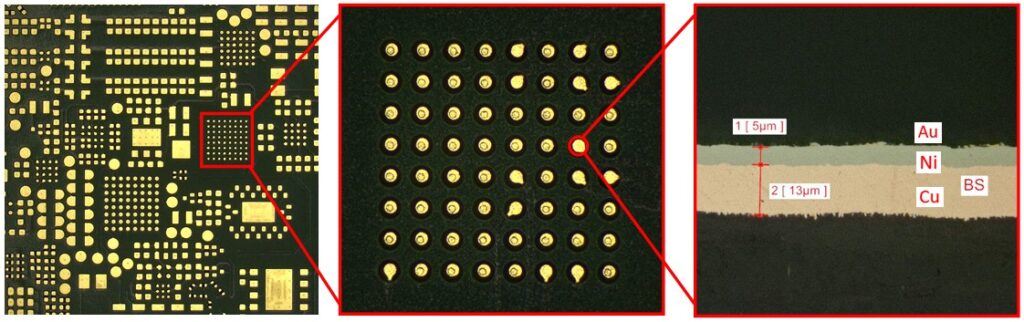
Mittlerweile haben wir diesen Auftrag schon mehrmals erfolgreich umgesetzt, sodass die Abläufe fest definiert sind. Sie haben auch ein herausforderndes Projekt? Kommen Sie gerne auf uns zu, wir freuen uns auf Ihre Anfrage!
Inhaltlich verantwortlich: Nikolas Koulouris